1. Refuse-Derived Fuel (RDF)
Household waste can be defined as solid waste comprising garbage and rubbish (bottles, cans, clothing, compost, woody waste material, disposables and non-recycled plastic, food packaging, food scraps, newspapers, magazines and yard trimmings, textiles, leather) that originate from private homes or apartments. It may also contain household hazardous waste. The approximate classification of MSW in a developing country is represented in Figure 1.

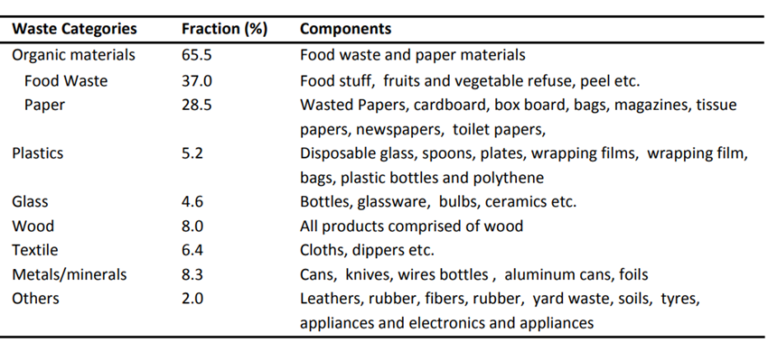
Figure 1: Composition of the MSW in developing country
In general, the decomposable materials in refuse are isolated from glass, metal, and other inorganic items through sorting and separating operations. These are carried out mechanically, using differences in such physical characteristics of the refuse as size, density, and magnetic properties. Such processes produce higher quality fuel products with a higher heating value than the initial waste (as shown in Figure 3).
Watch the video:
Machinex use innovative recycling solutions to design and produce custom-made sorting and recycling technology for facilities all around the world
Watch the video:
Macpresse is a world leader in pre-treatment of waste and recyclable materials, producing balers and special equipment
Watch the video:
BHS designs, manufactures and installs processing systems tailored to extract recyclables from the waste stream
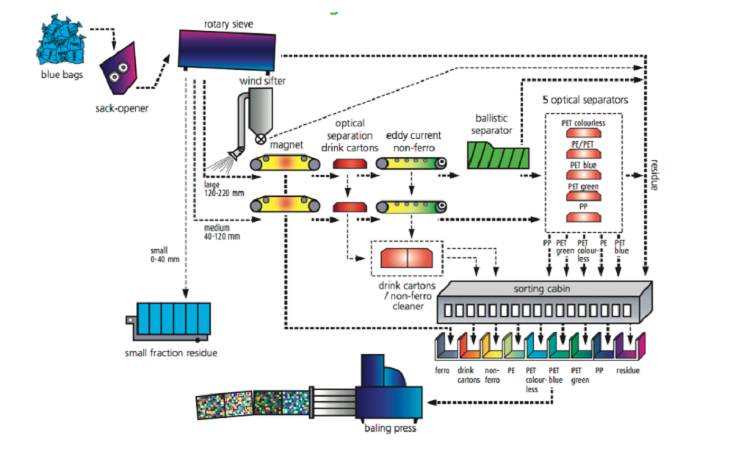
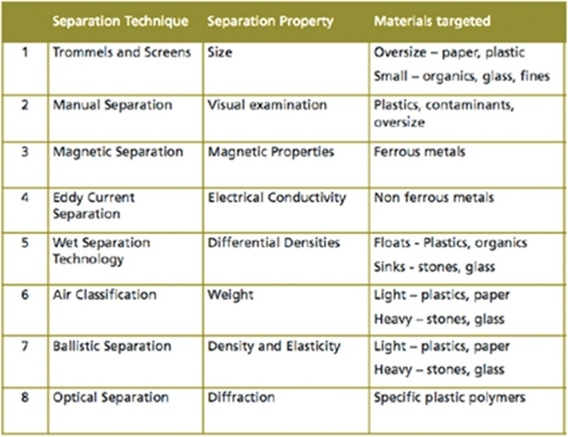
Figure 2: MSW pre-treatment techniques
RDF is not standardised and the properties of RDF (composition, contaminants, heating value) are undetermined. RDF is used as fuel for cement kilns or as feedstock for the WtV technologies, even though it does not fulfil the requirement for Solid Recovered Fuel (SRF).
Before the MSW can enter the RDF production process, commodities such as metal and glass should have been separated from cardboard, paper, plastics and food for recycling. The RDF preparation scheme includes the waste reduction size, separation, crushing and drying and pelletising as shown in Figure 2. The advantages of RDF are high calorific value and reduction in landfilling problems hence it is well developed throughout the Europe. While, the main disadvantage of the process is land acquisition, treatment equipment and manpower, which makes the process expensive.
Typically, 1 kg of MSW feed produces an output of 0.4 to 0.8 kg of RDF with a moisture content of 10-17%, 10-20% ash content and 15-25 MJ/kg calorific value. To make 1 kg of RDF, the glass, metal and moisture fractions must be removed from MSW and a higher concentration of paper, plastic and high-energy organics must be attained. The largest change in concentration is needed for plastics, which go from 12% in MSW to 31% in RDF. Separation, milling and drying operations consume 1.8 MJ of electricity per kg RDF.
Figure 3 shows how RDF and MSW look like and reports the composition of RDF and non-recyclable plastic waste.
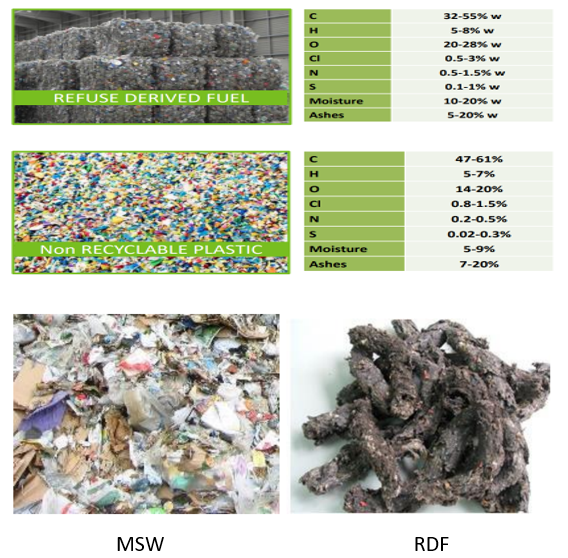
Figure 3: MSW to RDF
Depending on the level of mechanisation, CAPEX for a MSW to RDF plant is estimated to be 90-180 USD per tonne annual capacity for capacities between 20,000 and 100,000 tonnes/annum in 2017.
A gate fee or tipping fee is the charge levied upon a given quantity of waste received at a waste processing facility. The standard gate fee is $106 per tonne in the UK. The standard landfill tax in the UK and the Netherlands are respectively $118.7 and $13.8 per tonne waste.
1.2 Solid Recovered Fuel (SRF)
SRF is a much more refined resource compared with RDF and produced from non-hazardous waste which usually has undergone a prior sorting process according to EU standards (e.g. EN15359). It is typically produced from MSW, industrial and commercial waste or construction and demolition waste. For creating SRF the following separating technologies can be used:
- A series of magnets can extract ferrous metals
- An eddy current separator can extract aluminium that could damage the secondary shredder
- A vibration screen or trommel can sift out soils and fines
- An air separation box (wind shifter) can remove large lumps of materials
The technology can of course be configured to suit varied end user specifications, but a particle size of less than 30mm,moisture content of < 15% and a calorific value of 18-22MJ /kg appears to be the norm. Following this sophisticated SRF manufacturing process, the end product is a resource from which energy can be harnessed. Below figure presents the block flow diagram of the SRF production:

Figure 4: Simplified block flow diagram of an SRF production plant
Of the input MSW to a mechanical treatment plant, 72 wt% is recovered as SRF, equivalent to 86% energy recovery.
2. RDF or SRF Torrefaction
Biomass can be converted into char, coke and biochar which have similar properties to that of coal. Torrefaction is the mild pyrolysis process carried out in the absence of oxygen or in an inert atmosphere at 200-300 °C to produce biofuel with improved fuel characteristics; the torrefied solid biomass has high calorific value, low moisture content, lower O/C and H/C ratios and desirable properties such as grindability and high hydrophobicity.
The toasted biomass contains much of volatile matter and requires high residence time to reduce the volatile matter. Combustion reactions are suppressed because of low oxygen supply. Improved grindability reduces power cost required for size reduction and displacement. Additionally, the lower equilibrium moisture content of the torrefied biomass has the advantages of storage ease and higher heating value.
Gaseous products produced in torrefaction process are classified into permanent gas (CO and CO2) and condensable gas (acetic acid, formaldehyde, methanol and water). Torrefaction may be light, mild or severe based on the temperature input required to consume the lignocellulosic contents of the biomass. Some of the products received in torrefaction are H2, CO2, toluene and benzene, H2O, acetic acid, alcohols (methanol), aldehydes (formaldehyde), ketones, char and ash.
The increase in the torrefaction temperature results in decrease in energy yield percentage. The characteristics of fuel from food waste were studied in the temperature range 150-600 °C in a horizontal tubular reactor. The study concluded the optimum temperature range for food waste between 290 and 330 °C and showed the energy and mass yield of the food waste decreases with an increase in torrefaction temperature.
The sizes of solid wastes are generally not uniformly distributed and need to be brought to uniformity and optimum size for best reactor outputs. The smaller size of particles offer higher surface area and enhanced heat and mass transfer. A mixture of agricultural, forestry and industrial wastes was processed and crushed into particles of prescribed sizes. The reduction in size of particles enhanced the product quality. Particle size of 0.5 mm gasified in an entrained flow gasifier resulted in maximum fuel conversion. The effect of particle size on dry gas yield was studied with three municipal solid waste feeds of different size regimes, viz., less than 5 mm, 5-10 mm and 10-20 mm in a fixed bed reactor. Smaller particle size resulted in faster heating rates apparently for two reasons. One is the availability of larger effective heat transfer surface area during thermal treatment and the other was gas diffusion augmented reaction kinetics. The H2 and CO content increased with reduction in particle size.