1. Mixed Plastic Waste Pyrolysis
Plastics pyrolysis involves heating plastic waste to 400-600 °C in the absence of air. The liquid syncrude yield can be as high as 85 wt%, with the balance being light gases (H2 , CO, light hydrocarbons which can be used as process fuel) and solid carbonaceous char (which may contain metals and inorganics from the raw feed or the process). The syncrude yield is influenced by the feedstock, reactor temperature and residence time primarily, as well as any in situ catalyst that may be present.
Different polymer types react differently when aliphatics pyrolysed. For example, polystyrene (PS) and PMMA (Perspex) and Nylon depolymerise to monomers, whereas polyethylene and polypropylene (PP) ‘crack’ into mixtures of hydrocarbons. Polymers containing oxygen (e.g. polycarbonates, PET) give lower yields of hydrocarbons and may be more valuable if recycled independently; polymers containing chlorine, nitrogen and sulphur (e.g. PVC, polyurethane, nitriles) give hazardous by-products and again are best treated separately. Plant design and conditions reflect which polymers are in the feed.
Polyolefins (HDPE, LDPE, PP) which make up the bulk of raw mixed plastic waste are mostly used for WtF. Mechanical sorting/cleaning and shredding of mixed plastic waste are required to reduce contaminants (e.g. metals, PVC, PET, PS) and facilitate handling. Depending on contaminant levels, the pyrolysis plant may still need measures to dechlorinate the final product.
Thermal cracking of polyolefins generally gives a wide molecular weight distribution in the pyrolysis products, although this may be offset by plant design or use of catalysts. Depending on process conditions, it might be suitable to fractionate syncrude into transport fuels and heavier products. Polyolefin cracking generally gives a mixture containing perhaps 1:4 aromatics:aliphatics, with higher temperatures and longer residence times favouring aromatics but reducing the liquid yield. The aliphatics are a mixture of paraffins and olefins, both linear and branched. The balance depends on process conditions and feed composition; PP tends to be more reactive than PE.
Figure 13 depicts the schematic of this process.
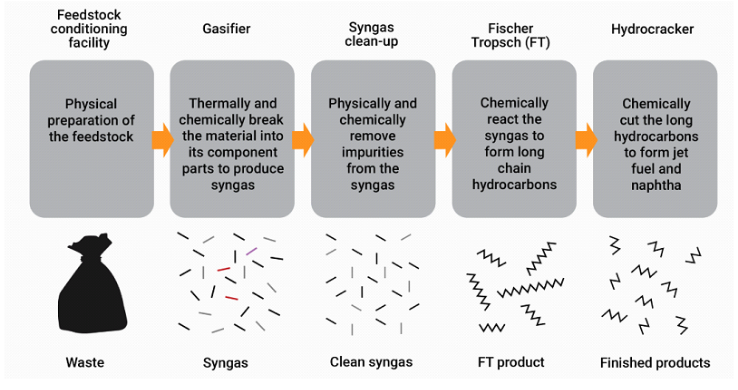
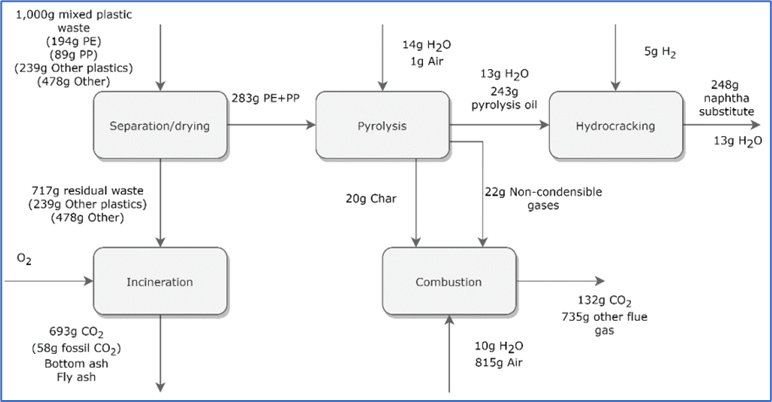
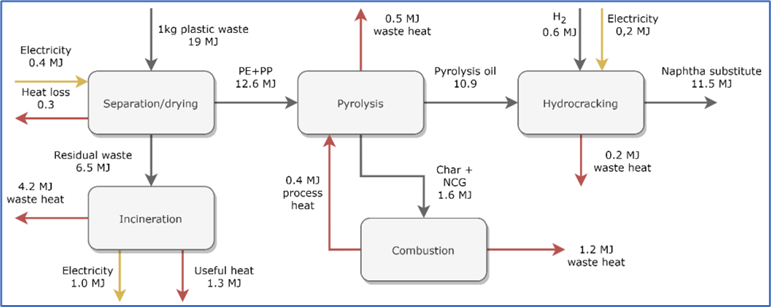
Figure 13: Schematic flow diagram for a typical MSW to fuel process
Information about impurity levels (e.g. residual oxygenates) and stability is sparse and likely to be case-specific, but in general, it is best to avoid plastics containing oxygen, such as PET. Entrained char particles are an issue with some biomass pyrolysis processes and might be linked to fouling or plugging of catalytic reactors used for upgrading. Cyclonic treatment of pyrolysis vapours seems to be accepted as suitable for removal of particles >10µm while ceramic membrane filters seems to be suitable for liquid treatments for particles <10µm.
Plant capacities are reported in the range 20-60 tonnes/day fuel, with potential to scale up to perhaps 300 tonnes/day. In contrast, a notional EU refinery would make several thousand tonnes/day of gasoline or diesel, so a single pyrolysis plant would be unlikely to supply more than 5-10 % of total fuel product. This suggests a hub model where several pyrolysis plants supply syncrude to a single refinery.
Most of the current plants make products for fuel blending, so the quality of pyrolysis products is acceptable for low level blending; all that may be required is fractionation into the right boiling range. The olefinicity might pose a fouling risk for conventional distillation.
At higher blend levels, the following parameters might need closer scrutiny:
- Although the octane rating of diesel fraction is good, the impurities such as metals, nitrogen, oxygen and especially sulphur and di-olefins are concern.
- Aromatics and olefin content of diesel fraction as indicated by Bromine Number
2. MSW Gasification and Fischer Tropsch Synthesis
Conversion of MSW to synthetic refinery feedstocks (syncrude) or transport fuels has two major steps:
- Gasification of MSW to syngas
- Conversion of syngas into products via Fischer-Tropsch (FT) synthesis
Synthesis reactions usually require a syngas which is richer in hydrogen; therefore, plants include syngas cleaning and a follow on catalytic shift-reactor to adjust the CO/H2 ratio. The process requires oxygen or air, sometimes supplemented by steam, which enhances shift in the gas phase. The heat needed for gasification is usually provided by combustion of some feedstock within the gasifier or by external combustion of unwanted by-products such as char/fuel gas.
There are several types of gasifiers (Circulating Fluidised Bed (CFB), Entrained Flow), which differ in terms of solids-handling, air/oxygen/steam injection, operating temperature and pressure, tar and ash/slag management. Engineering issues such as inherent heat/mass transfer limitations, solids handling, ancillary equipment (e.g. air separation) influence the scale for individual gasifiers as shown in Figure 14.
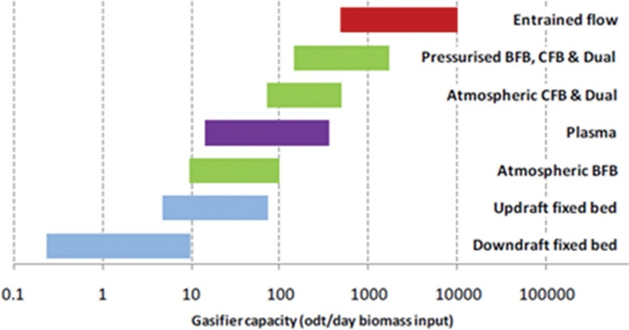
Figure 14: Capacity range for different biomass gasifier technologies
The preferred designs for gasifying biomass are entrained flow, fluidised bed (FB) and plasma gasifiers. Entrained flow gasifiers require fairly uniform feedstock (torrefied and milled feedstock) and can operate at high pressures. Plasma gasifiers operate at very high temperatures and are costly to build and operate. Fluidised bed and plasma gasifiers are mostly designed for low operating pressures; therefore, for further processing of syngas require compression.
Synthesis gas cleaning and conditioning is key for successful integration of gasification and FT technology. Raw synthesis gas contains impurities such as particulates, metals, chlorine, and sulphur which must be removed for both power and synthesis applications; the latter are more stringent. Tars also may be an issue with solid and liquid gasifier feeds, so some systems include catalytic tar conversion. In some cases, the synthesis gas CO:H2 ratio must be adjusted to better suit the FT conversion technology; this is commonly carried out using water-gas shift catalysis.
3. FT Synthesis
FT synthesis is an established catalyst process to convert H2-rich syngas into hydrocarbon liquids. It is conventionally operated at 20-40 bar and 200-250 °C (Cobalt-based catalyst) or 300-350 °C (Iron-based catalyst). The primary product is a wide boiling range syncrude comprising mainly linear aliphatic hydrocarbons with carbon-numbers in the range 4 to >40 with a boiling range of 40 °C to >500 °C.
Operational world scale FT-plants include Shell’s Pearl Gas-to-Liquids (GTL) plant in Qatar and Sasol’s Secunda Coal-to-Liquids (CTL) plant in South Africa; both produce ca 140 kbbl/day (ca 15 kton/day) of liquids. The FT reaction is very exothermic, consequently the reactor must be able to handle large heat flux, which limits the capacity of individual FT reactors to roughly 500 to 2000 ton/day depending on technology; therefore, large facilities may have several trains of FT reactors.
3.1 Wax Hydrocracking
Typical FT-syncrude contains roughly equal parts of naphtha-range, diesel-range and high- boiling materials; however, because they primarily comprise linear hydrocarbons they have high melting points and are generally unsuitable for fuels. Therefore, FT-syncrude is commonly hydrocracked to convert the high-boiling fraction into gasoline and diesel; this simultaneously isomerises the products to improve their low-temperature properties.
In principle, it resembles the hydrocracking processes used in crude-oil refineries, but is optimised for cracking linear paraffins rather than the mixed paraffins and substituted aromatics found in refinery streams. FT-wax contains lower levels of contaminants (S, N, metals) than would be expected in refinery streams.
The FT technology landscape is complex, with a range of catalyst technologies (e.g. Fe-based, Co-based), process technologies (e.g. multi-tube, fluid-bed, modular) and a corresponding range of technology developers/providers/owners in a variety of different partnerships (e.g. Shell, Sasol, BP, Exxon, Johnson Matthey, Velocys, Axens).
3.2 Conversion Product
The FT-products may come in two forms, depending on the design of the FT process in the primary conversion plant:
- FT without hydrocracking makes a wide-boiling syncrude
- FT with hydrocracking makes finished FT-naphtha and FT-diesel. At present, FT-diesel and FT-naphtha already enter the refined product supply chain, but FT-syncrude generally does not.
In principle, FT-syncrude could be used as co-feed to the refinery CDU, i.e. it would be treated as a low-sulphur paraffinic crude. The lighter FT-fractions would go with the straight-run naphtha, kerosene, and diesel as they made their way through the refinery; being mainly linear paraffins, they would not react, so they might unnecessarily take up hydro-desulphurisation capacity.
Running FT-syncrude to the CDU might be considered as high-risk because any disruption to the CDU affects the whole operation of the refinery. There might be other entry points for syncrude, e.g. direct to conversion units such as FCC (fluid catalytic cracking) and hydrocracking. FCC is generally considered the more robust unit, but its yields and product qualities are poorer.
A WTF facility could be co-located at a refinery with direct integration with refinery conversion processes and utilities. This would allow use of all FT products from LPG to heavy wax, and integration regarding utilities, hydrogen, etc.
Watch this video:
Biomass to liquids Process which explains the process of converting biomass into syncrude.
Watch this video:
Fulcrum has developed a proprietary, patented and proven technology for converting landfill wastes into net-zero carbon transportation fuels.
Velocys has demonstrated a waste to fuel technology.
Watch this video:
Shell has developed IH² (Integrated Hydropyrolysis and Hydroconversion) technology Which is a catalytic thermochemical process for converting a broad spectrum of organic wastes to liquid hydrocarbons.
3.3 CO2 Emission
As per gasification of MSW, water-gas shift reaction and FT reaction (shown below), WtF technologies produce less CO2 than WtE and WtH technologies and more than WtM technology.
CO + H2O —> CO2 + H2
nCO + (2n+1)H2 —> CnH2n+2 + nH2O
_____________________________________________________________________________________________
(3n+1)CO + (n+1)H2O —> (2n+1)CO2 + CnH2n+2
n>=4
for n=8 25CO + 9H2O —> 17CO2 + C8H18 or CO + 0.36H2O —> 0.68CO2 + 0.04C8H18