Figure 6 shows a process flowchart of the general steps in waste incineration. In a modern WtE plant, municipal solid waste is delivered to the site and stored in a bunker. A crane thoroughly mixes and feeds the waste into the feed hopper. From there it is pushed onto the grate by a ram feeder. A fully integrated control system ensures stable and efficient operation and optimises the fire position on the grate. Once combustion is complete, the inert ash that remains falls into the bottom ash extractor, from where it can be taken to a bunker or storage area for metals recovery and further use.
The gases released from the waste are mixed with secondary air and recirculated flue gases above the grate. This assures complete combustion and the lowest CO, NOx and Volatile Organic Compounds (VOCs) emissions. Recirculation of flue gases also increases the plant’s energy efficiency. The energy released is used to produce superheated steam, which is expanded in a turbine generator to generate electricity. Flue gases are then cleaned to the strictest standards, and are continuously monitored before being released at the stack.
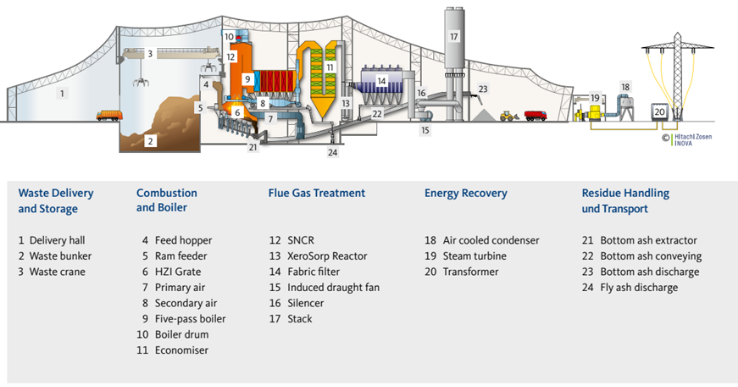
Figure 6: Process flowchart of waste incineration
Due to the wide variety of substances present in the input waste, untreated flue gasses from waste incinerators can contain harmful emissions including but not limited to: heavy metals, dioxins, furans, carbon monoxide, hydrogen chloride, hydrogen fluoride, sulphur dioxide and nitrous oxides. To limit the emission of pollutants, electrostatic precipitators (E-filters), and baghouse filters, often combined with the use of activate carbon, calcium carbonate or sodium bicarbonate as part of a multistage scrubbing process are used. DeNOx treatment systems are also utilized.
In order to reduce the net CO2 emissions to the atmosphere, the CO2 can be captured via post-combustion carbon capture by MEA, hot potassium carbonate and Metal-Organic Frameworks (MOFs). The captured CO2 is compressed and dehydrated before being transported to be:
- utilised for artificial fertilisation of crops in greenhouse horticulture
- injected into deep geological formations (including depleted oil and gas reservoirs or saline formations) which traps the CO2 for permanent storage
- utilised for feedstock to an urea plant
- utilised to treat and stabilise thermal residues (bottom ashes, boiler ashes, fly ashes, flue gas treatment air pollution control residues, drosses from slags, mineral by-product), and in turn valorise them into manufactured limestone (calcium carbonate) aggregate
Watch the video:
Hitachi Zosen Inova (HZI) is a global cleantech company operating in energy from waste (EfW) and renewable gas based in Switzerland.
Watch the video :
Watch the video:
Viridor plant built by CNIM MARTIN, specializes in the engineering and delivery of turnkey plants for the thermal treatment of waste and biomass.
As per combustion reaction of MSW (C + O2 —> CO2), WtE technologies produce the maximum CO2 compared to the other WtV technologies. Therefore, CO2 Capture, Utilisation and Storage (CCUS) cost of the WtE technologies is the highest amongst all other WtV technologies.