WtV technologies have been developed in the context of the circular economy for large capacity MSW conversion using thermochemical methods including torrefaction, pyrolysis, gasification, water-gas shift reaction, syngas reactions and combustion.
Energy yield of the WtV technologies depends on the feedstock composition, the targeted CO2 capture and maximum budget.
1. Pyrolysis
Pyrolysis is a tertiary recycling techniques widely used for thermal conversion of plastic waste at different temperature ranges from 300 0C to 900 0C. However, most of the researcher reported that optimum temperature for pyrolysis was 450 0C to 550 0C. Plastic waste pyrolysis is carried out in the absence of oxygen forming vapours and char. Vapours produced during pyrolysis are converted into liquid fuel by condensation process. The pyrolysis process can be optimized by using catalyst to reduce the temperature and retention time of process.
Some of the well-known licensors for pyrolysis technology are Klean Industries, Lummus (Green Circle), OMV and Pryme.
2. Gasification
Gasification is a process in which biomass is burnt in limited supply of air or oxygen (partially oxidised) to generate syngas. Syngas is composed of H2, CO, CH4 and CO2 with certain by-products including H2S, COS, CS2, NH3 and HCN (depends on feed). The temperature range of gasification is generally between 600 and 1200 °C. The syngas can be used as a direct fuel or can be converted into profitable products such as H2, synthetic natural gas (via methanation reaction), syncrude (via Fischer-Tropsch reaction), methanol and dimethyl ether. Below figure shows different routes for the syngas product of the gasification process.
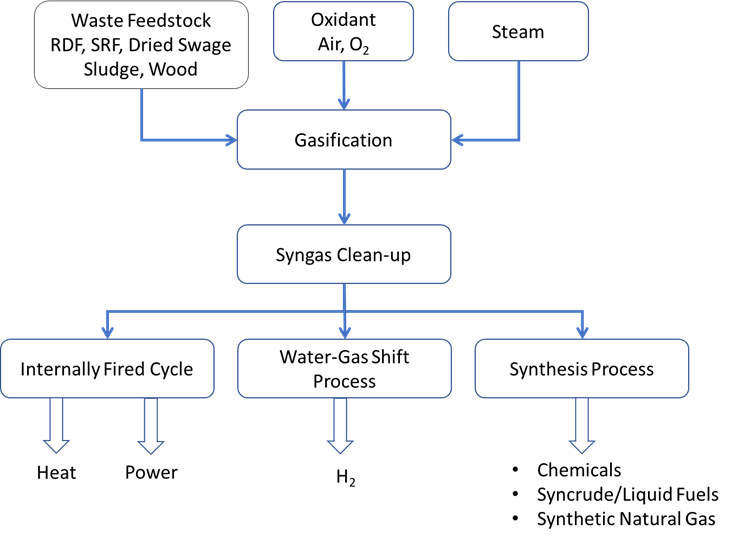
Figure 5: Different routes for the syngas product of the gasification process
The product consists of mixture of gases depending on various parameters such as gasifying agent, type of gasifiers used, equivalence ratio (an indication of oxygen flowrate), temperature, feedstock particle size, moisture content and catalyst. The gasification process is further classified into steam gasification, supercritical water gasification and catalytic gasification depending on the gasifying agent. The main drawback of using syngas for downstream application is high concentration of impurities such as tar, particulates, alkali chloride and sulphur species. Various hot syngas clean-up systems have been developed for the removal of such impurities.
The tar yield and tar concentration decrease with increase in temperature in a downdraft fixed bed gasifier for temperatures in the range of 700-900 °C. The downdraft gasifier minimizes tar content in the product compare to the other type of gasifier.
In the gasification of municipal solid waste using a circulating fluidised bed gasifier, char gasification and steam reforming are restricted in the range of 500-650 °C, and increasing temperature range from 650 to 900 °C leads to maximum carbon efficiency and hydrogen production.
The comparison between fluidised bed gasifier at low temperature (870 °C) and entrained flow gasifier at elevated temperature (1300 °C) showed that the entrained flow gasifier requires extra investment when compared to the fluidised bed gasifier.
The economic feasibility of the fluidised bed gasifier and entrained flow gasifiers for biomass gasification process shows that the economic efficiency of entrained flow gasifier was 11% higher than that of fluidised flow gasifier.
Some of the well-known licensors for gasification technology are Choren, Uhde, JFE, Shell, TRI, Inentec, Siemens and MHI.
3. Combustion
In combustion technology, heat is the main product and yield depends upon feedstock, gasifier and temperature (750-1500 °C). Almost all solid wastes can be treated using combustion. Other than electricity production, combustion is also used for drying, pre-heating and steam generation in industries. The carbon-based materials like coal are majorly used for production of energy, releasing large amount of CO2 to the environment.